Sooner or later, any master has a situation when the number of purchased instruments requires their systematization and ordering. For this purpose, various organizers, drawers and cabinets are used. This article will discuss their varieties, advantages and disadvantages, and also will be given several master classes on making a tool box with your own hands, drawings and step by step are given instructions.
Read in the article
- 1 Tool organizer requirements
- 2 Overview of the different types of tool boxes
- 2.1 Boxes
- 2.2 Cases
- 2.3 Organizer
- 2.4 Trays
- 2.5 Containers
- 2.6 Multiboxes
- 2.7 Chests of drawers
- 2.8 Maxi boxes
- 3 Wooden tool box
- 3.1 Materials and tools
- 4 Plywood tool box
- 4.1 Materials and tools
- 5 Metal tool box
- 5.1 Materials and tools
- 6 Tool box on wheels
- 7 Original ideas for homemade tool boxes
- 8 Summing up
Tool organizer requirements
When choosing a finished product or materials and design for making an organizer for tools with your own hands, you should take into account some specific requirements:
- The bottom, or better the entire lower part of the box, must be monolithic or have particularly reliable fasteners. The product will have to withstand significant weight.
- The base must be stable under any load of the internal volume.
- Feet should be made of foam rubber or other similar material so as not to damage the surface on which the box will be installed.
- If the walls are made of elastic or deformable materials, they must have stiffening ribs so that when the box is fully loaded, it does not change shape.
- In the presence of moving parts: folding system, closing doors, drawers, all transformations should take place without the application of effort, including with partial loading of the moved containers.
- The body of the box, as well as all its internal compartments and structural elements, must not have gaps. The cover should fit snugly, have additional fixation in the form of latches or locks.
Each of the materials used to make a toolbox with your own hands is subject to stricter requirements for strength and durability:
- wood, plywood - processed with antiseptic and flame retardant impregnations or primers;
- metal - galvanized sheet is used or the product is painted with shock-resistant oil paints;
- polymers - Impact-resistant plastic is used that can withstand a wide range of operating temperatures. Typically, these are polyurethane, PVC, extruded or cross-linked polyethylene.
Overview of the different types of tool boxes
Manufacturers offer a wide range of cases, drawers, organizers and tool boxes. There is no strict classification of their design. Most often, tool organizers are distributed according to purpose, material of manufacture, size and method of opening.
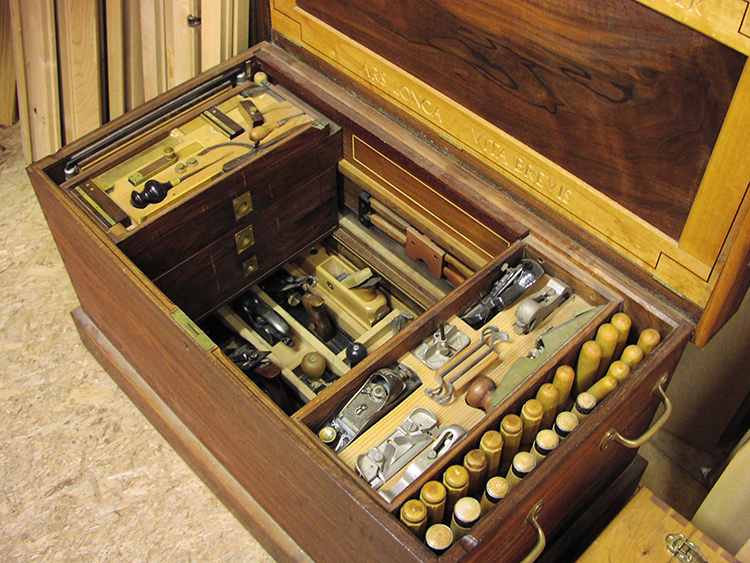
There are also professional boxes, as a rule, they have a large volume. These are metal structures or made of extra strong plastic, on wheels. They usually have a separate place for each instrument - a lodgment. Household boxes are more versatile, they are small in size, the inner space is divided into sections of various sizes, some have removable or movable partitions, there are places for storing consumables (nuts, bolts, screws).
Boxes
Capacious closed-type structures in the form of a rectangular box. As a rule, they are equipped with a lid that can be folded back, removed completely or moved apart. It usually provides an organizer for hardware. Covers are equipped with latches, less often with locks. Depending on the volume of the box, it can be equipped with a carrying handle or wheels.
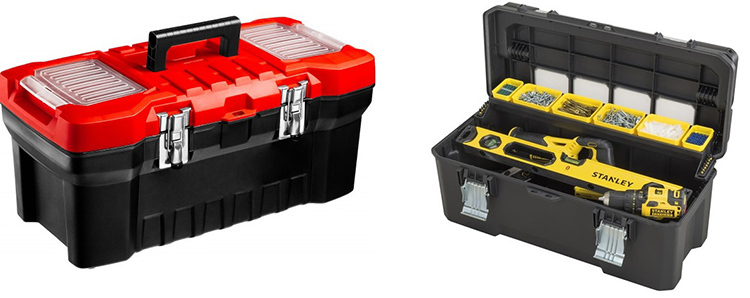
Cases
Outwardly, it looks like a standard medium-sized suitcase. Inside, there is usually a foam lodgment or a semi-rigid base with clamps - elastic loops, plastic clips, etc. Typically used for a special set: locksmith, automotive and others. Thanks to well-thought-out ergonomics, despite its compact size, it contains a large number of tools.
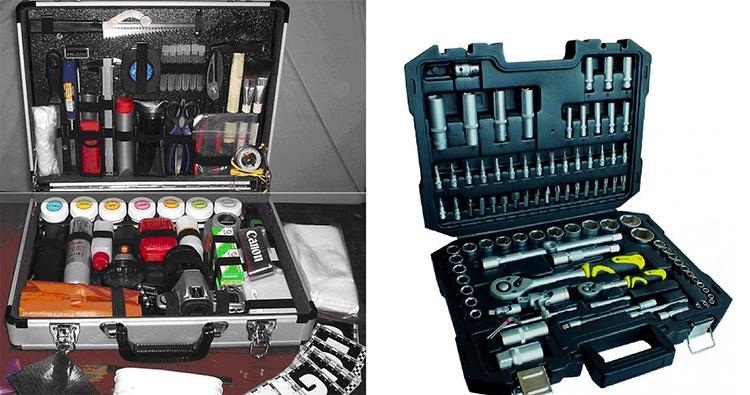
Organizer
A small box, the interior of which is divided into many small cells. Used for storing small items, fasteners and other hardware. The shape can be horizontal, then the organizer resembles a case, or vertical in the form of a small chest of drawers.
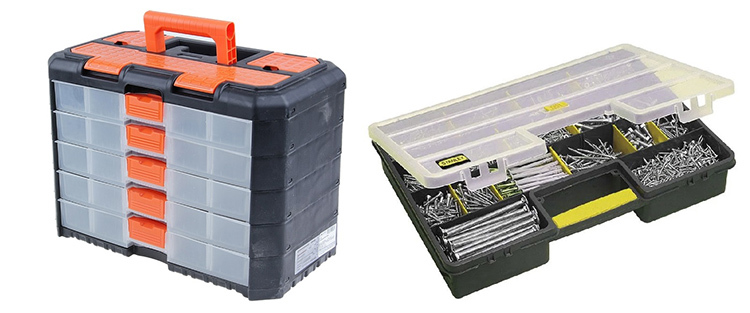
Trays
They belong to open-type containers. The tools are always visible in the direct quick access area. However, objects inside may fall out during transport. As a rule, trays are used permanently in the workshop and do not have a handle. And portable models are equipped with a weak and uncomfortable handle that can tear during carrying.
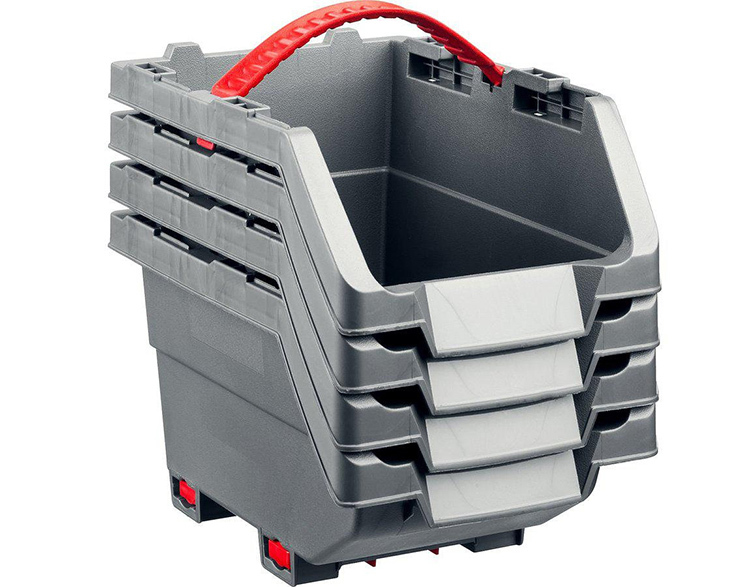
Containers
Quite large containers with a closing lid, sometimes with compartments for hardware. Inside, they either have no partitions at all, or are divided into 2-3 large sections. Used to store or move oversized tools. Carrying handles are located on the sides of the container. The handle on the lid is needed to remove it; it is better not to use it to carry it in order to avoid damage to the locking mechanisms.

Multiboxes
By design, it is a cross between vertical organizers and chests of drawers. They are compact in size, equipped with a carrying handle, consist of three or more containers of the same size, located one above the other and sliding out like drawers. They are used both for storing a large number of hardware and for placing various tools.

Chests of drawers
They differ from multiboxes in large dimensions and boxes of various sizes. As a rule, they are used permanently for storing tools in a workshop. They are usually handmade from wood or plywood.

Maxi boxes
Refers to professional equipment. They are of considerable size, therefore they are supplied with wheels for transportation or movement around the workshop. Inside, they are divided into sections, have compartments for oversized tools, organizers for hardware and other, larger consumables.
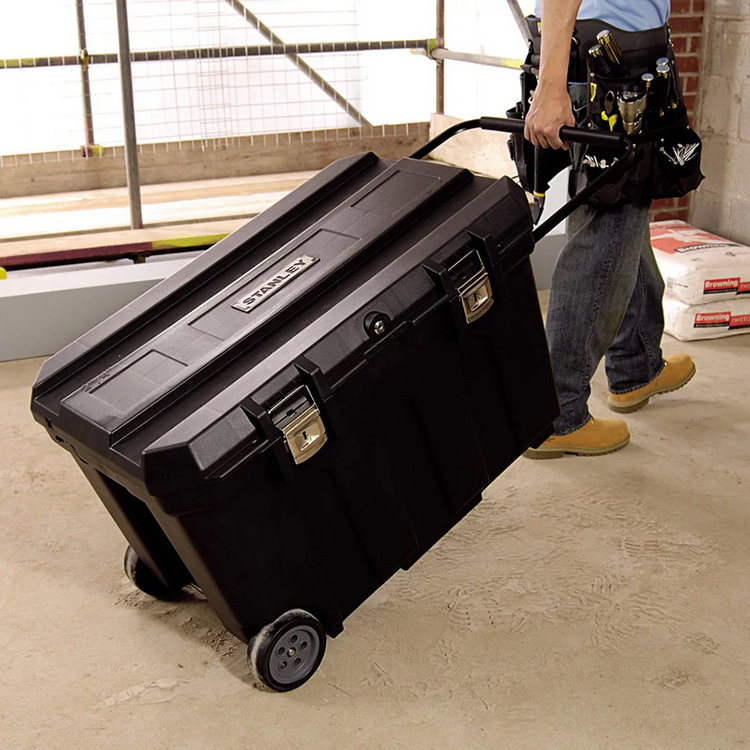
Wooden tool box
The compact wooden box is useful not only for storage, but also for carrying tools. The absence of a cover will provide quick access to all items inside. The choice of solid wood as a material of manufacture is dictated by such advantages as availability and ease of processing.
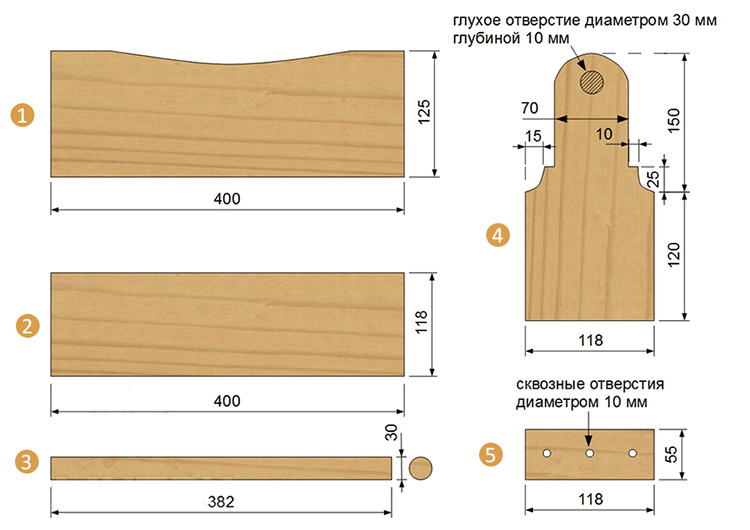
Materials and tools
For manufacturing, you will need the following tools and materials:
- planed edged board 15-20 mm thick;
- self-tapping screws for wood 25 × 3.5 mm;
- jigsaw;
- drill;
- screwdriver;
- clamp.
Illustration | Description of action |
![]() | Transferring all dimensions to the board |
![]() | Using a jigsaw, blanks are cut |
![]() | We fix the constituent elements with a clamp and fix them with screws |
![]() | We drill the corresponding holes in the board to accommodate the screwdrivers |
![]() | We insert a handle into the blind holes (you can use a cut from a shovel) and fix the second end wall |
Plywood tool box
The edged board can be replaced with 10 mm moisture resistant plywood. This material is more durable with less weight and thickness. However, making plywood boxes requires certain skills.
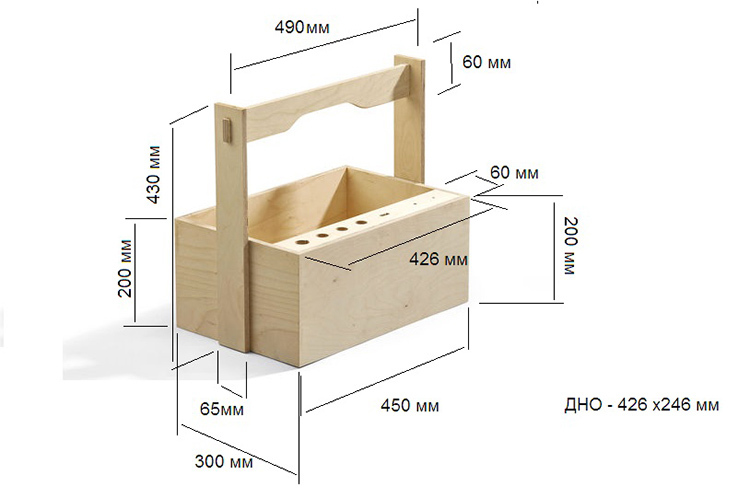
Materials and tools
Making a tool box will require the following materials and tools:
- plywood 10-12 mm;
- joiner's glue;
- wood screws or universal 15 × 2.5 mm or nails 20-25 mm;
- wood varnish;
- jigsaw with a variable ski position (some of the cuts must be made at an angle of 45º);
- Phillips screwdriver or hammer;
- drill with a set of wood drills;
- clamps.
IMPORTANT! Both screws and nails can be used as fasteners. To use screws, it is necessary to pre-drill holes of the appropriate diameter so that the plywood does not crack. Nails can be used without preliminary preparation, but they have much less fixing effect.
Illustration | Description of action |
![]() | According to the dimensions indicated in the diagram, we cut out 4 walls of the box. 450 × 200 mm long sides, 300 × 200 mm short (side) sides. The end edges of the walls that will be attached to each other must be cut at an angle of 45º |
![]() | We glue the cuts with PVA-based wood glue |
![]() | We carefully fold them together so that there are no distortions. For convenience, while drying, we strengthen the corners with tape. Leave it to dry for a few hours. At the bottom of the box we nail the slats 15 × 15 mm² |
![]() | Cut out the bottom of the box 426 × 246 mm. We grease the slats with glue and lay the bottom on them. For a tighter fit, you can put a hammer or other heavy objects on the bottom |
![]() | A place for a grip and spikes are cut in the handle. The cleat width should be 40 mm and depth 20 mm |
![]() | Cut out pen holders 430 × 65 mm. Selecting the groove for the tenon in the holders. To do this, draw a pencil around the contour of the thorn. We drill two holes. We connect them with a file and give the shape of a rectangle |
![]() | Use a file to adjust the size of the spike so that it fits snugly into the groove. For additional fastening during assembly, grease it with glue. |
![]() | Using a drill with a stop in the drawer wall and in the handle holder, we drill blind holes 6-8 mm deep. Then wooden dowels are placed on the glue. |
![]() | We apply joiner's glue to the joints of all parts and fix the assembled structure with clamps |
![]() | In the side toolbar, we drill holes for the most used tools: chisels, screwdrivers, drills, cutters, etc. |
![]() | We cover the product with varnish to protect it from moisture |
Metal tool box
If there are several scraps of tin lying around in your workshop, you can make metal boxes from them for storing various small parts, hardware and accessories. It is better to place such containers on shelves or workbenches. They provide direct access to content.
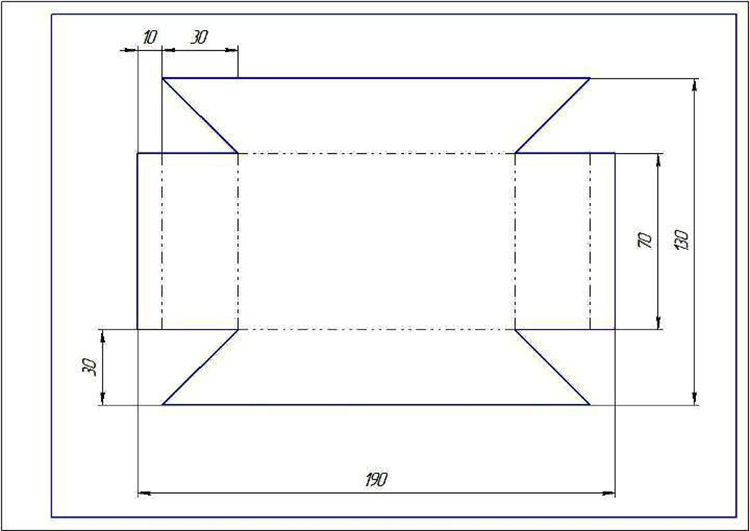
Materials and tools
To make metal boxes, you do not need power tools and special locksmith skills. The main advantage of such a product is its extreme simplicity. A dozen of these boxes can be made in a few hours. For work you will need:
- galvanized sheet with a thickness of 0.5-1.5 mm;
- scissors for metal;
- a hammer;
- an anvil or any metal bar.
Illustration | Description of action |
![]() | Choose a large enough piece of tin and transfer the markings to it |
![]() | We cut out the workpiece according to the markings using metal scissors. Tin with a thickness of more than 1.5 mm can be cut with a grinder, the shape of the pattern allows you to get around to all corners |
![]() | Using a hammer and anvil, the sidewalls are bent |
![]() | Then the petals of the long sides and the upper part are wrapped, a kind of envelope is obtained |
![]() | By proportionally changing the dimensions in the drawing, you can get boxes of different capacities |
Tool box on wheels
The next project is much more difficult. To implement it, you will need a rather expensive tool and a sufficient level of skills to work with it.
Tools:
- welding machine;
- Bulgarian;
- drill;
Materials:
- metal profile: equal-flange angle 30 × 30 × 2.5 mm - 6 m; square pipe 20 × 20 × 1.5 - 4 m; square pipe 15 × 15 × 1.5 - 6 m;
- plywood (10 mm) - sheet 1.5 × 2.0 m;
- aluminum profile (can be replaced with a CD drywall profile): corner 50 × 20 × 2 mm - 6 m; p-profile 20 × 20 × 2 mm - 1m;
- furniture guides for drawers 45 cm - 3 pairs;
- rotating wheels - 4 pcs;
- consumables: screws, bolts, paint.
Illustration | Description of action |
![]() | Three shelves with dimensions 1200 × 750 mm are made from a steel corner, the connection is made by electric welding |
![]() | For the frame of the side walls, a profiled tube 20 × 20 mm² is used. To get a rounding with a radius of 100 mm, you need to make 14-16 "cuts" (after 10 mm) with a grinder with a circle 2 mm thick |
![]() | The resulting workpiece is placed in a template with an internal distance of 750 mm. Then the slots are welded |
![]() | Shelves are welded to the side uprights |
![]() | Plywood is cut out:
The final size depends on the thickness of the plywood you are using |
![]() | From a square pipe 15 × 15 mm² we weld three supporting bases for the shelves |
![]() | We make sides for boxes from an aluminum corner 50 × 20 mm. Fastening to the base with rivets |
![]() | We install plywood on the bottom, and fasten the guides to the sides |
![]() | Handles are made of aluminum p-profile |
![]() | Handles are screwed to drawer fronts |
1 out of 4

What happened in the end
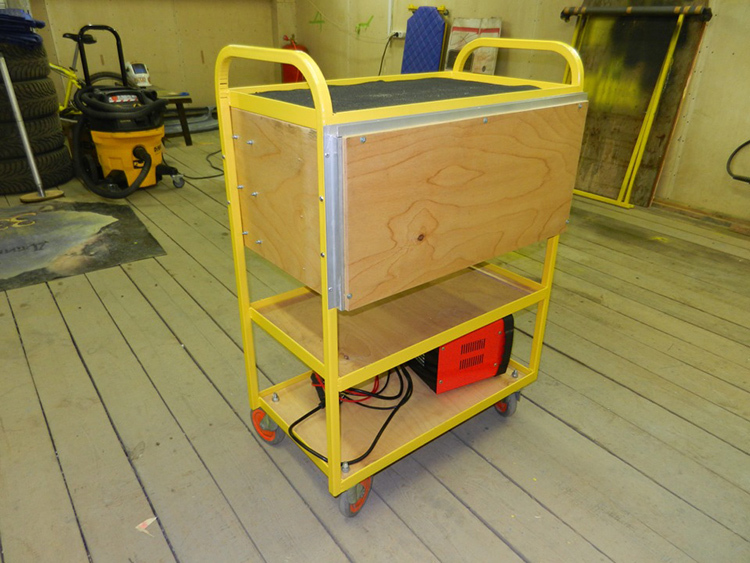

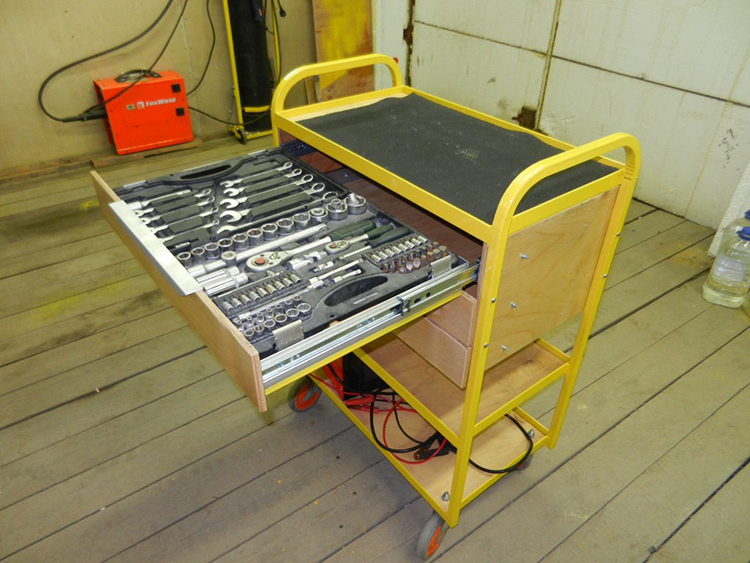
Video instruction of the manufacturing process:
Original ideas for homemade tool boxes
A lot of tool boxes, portable boxes and lockers are made by craftsmen from scrap materials. Quite original and functional designs are obtained.
The photo below shows unusual homemade tool boxes.
1 out of 6
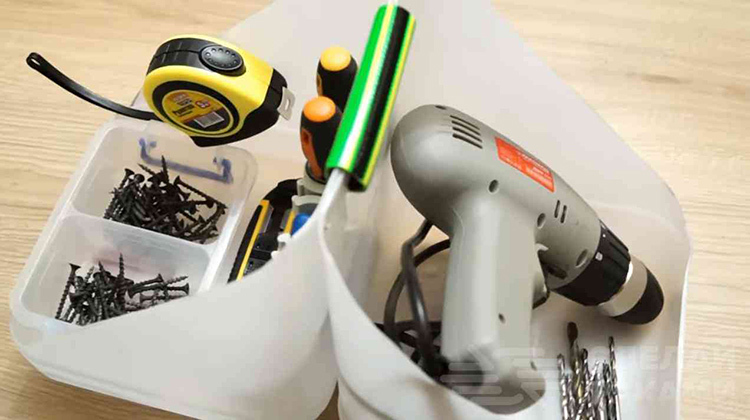
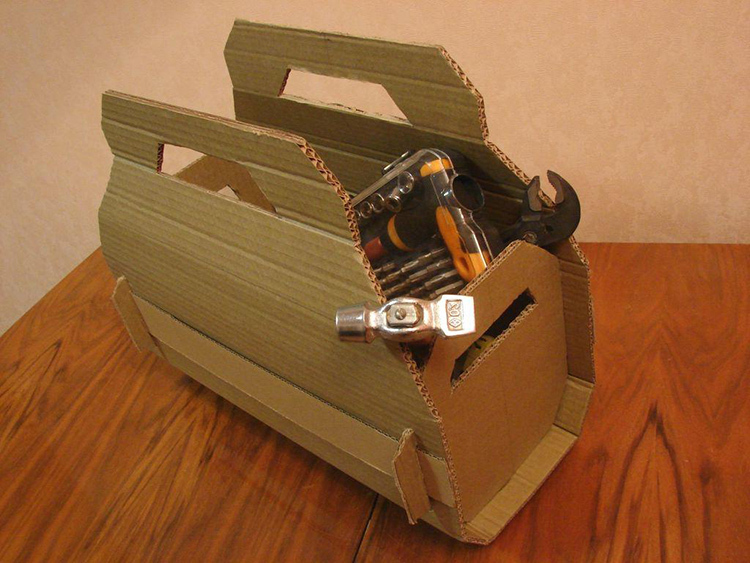
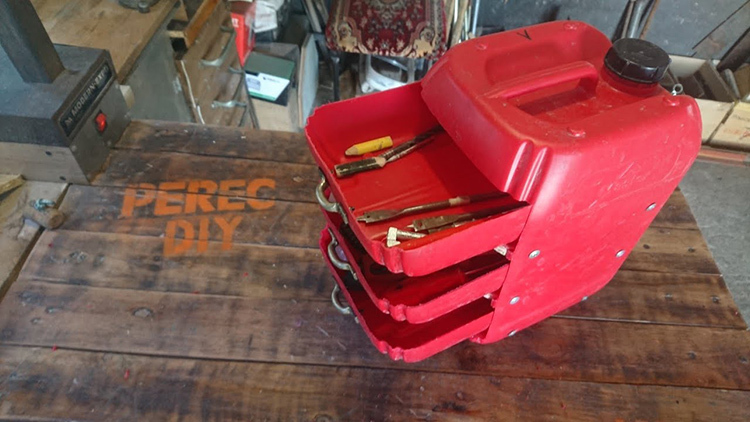


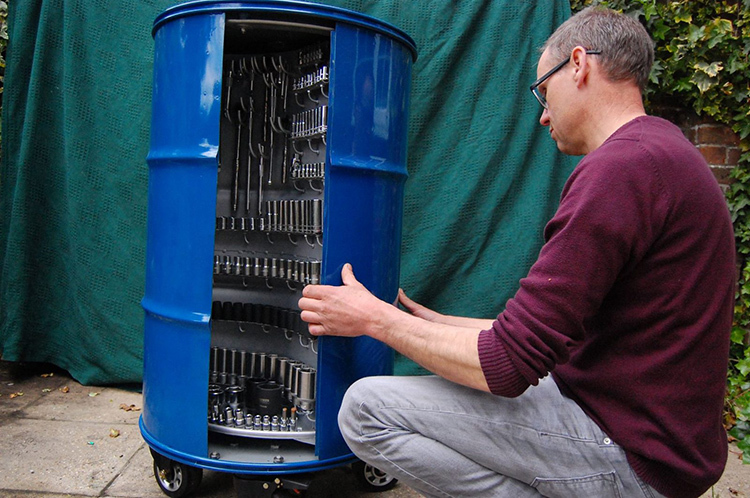
Summing up
It is safe to say that it is economically profitable to independently produce only fairly complex stationary or the simplest tool boxes, subject to the availability of a shareware material. The manufacture of portable boxes of a complex design from purchased materials, at best, will cost the same amount as a store box, or even much more expensive.
If you liked our article, you can share the link to it with your friends.