Various heat-insulating materials with a cellular structure are sold on the market, one of them is penoizol. It differs from others in that an ordinary person can mount or manufacture an installation that allows organizing the production of penoizol. Penoizol is a heater made of urea resin as a result of foaming. These materials are widely used in Russia, they are known as - "Mipora", "Mettemplast" or "Unipor".

Penoizol is a functional and inexpensive insulation material, the manufacture of which requires simple equipment and inexpensive raw materials. Therefore, it is inexpensive.
Pros and cons of the material
Outwardly, penoizol is very similar to marshmallows - it is white, porous, elastic and airy. The foamy mass after manufacturing allows you to insulate a building under construction as a result of filling air voids and hollow floors and walls, it eliminates any cracks and cracks. After solidification, the mass becomes a porous heat-insulating material that fills any free space.
Penoizol has several important advantages:
- The material is very durable, it is economical and lasts a long time. On average, the service life of thermal insulation is 50-70 years;
- Reduced thermal conductivity, makes it possible to keep heat in the house, significantly reduce energy and heating costs;
- Versatility of use, they can insulate the floor, roof or foam walls;
- The penoizol layer allows air to pass through well, the material does not accumulate moisture, it “breathes”;
- Not flammable, under the influence of high temperature the layer simply evaporates gradually;
- Rats and mice do not like him and avoid him;
- Fungus and mold do not develop on it;
- Does not decompose under the influence of chemicals and organic solvents;
- Environmentally friendly insulation, will not harm human health.
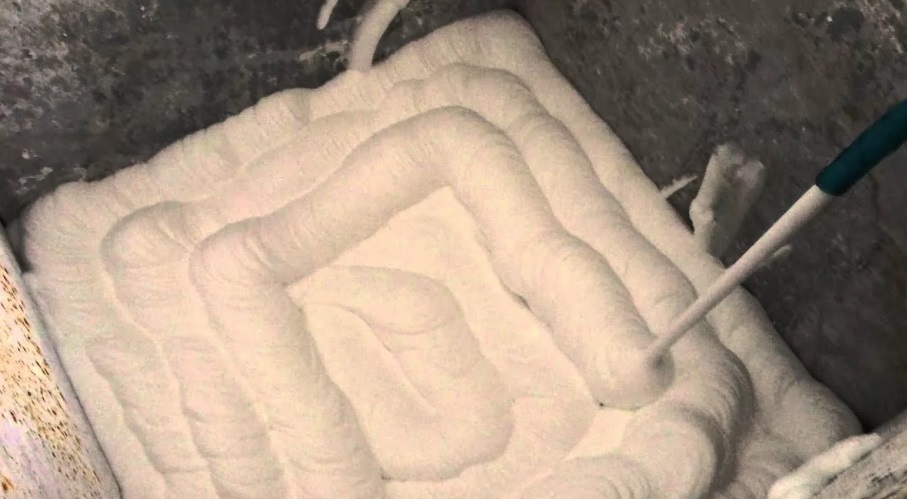
If we compare it with the usual heat insulators, then penoizol has many positive qualities. The main ones include:
- Thermal conductivity. The minimum indicator is 0.041 W / m / K, a layer of 10 cm thick is enough for such insulation;
- Noise protection. Sound absorption about 65%;
- High temperature resistant. Refers to G1 flammability group, B2 flammability category. This says that when exposed to fire, the material does not melt. During a fire, penoizol evaporates without forming toxic substances. Compared to foam, there is 10 times less smoke;
- Chemical resistance. Does not react to aggressive influences;
- Moisture resistance. It absorbs moisture well, but also gives it away. At the same time, it does not lose its positive properties, it can absorb up to 20% moisture, after which it evaporates. To prevent the appearance of mold, it is necessary to provide a ventilation gap when laying;
- Water vapor permeability. It is hygroscopic, allowing the walls to breathe. In the thickness of the wall, air circulates without obstruction.

Like any heat insulator, penoizol has its drawbacks. It is prone to shrinkage, this figure reaches 0.1-5%. This disadvantage is less in the material that fills the voids between the walls, when it expands, it turns out to be under slight pressure. During the drying of the foam, if the technology is violated and the use of low-quality raw materials, an unpleasant odor may appear.
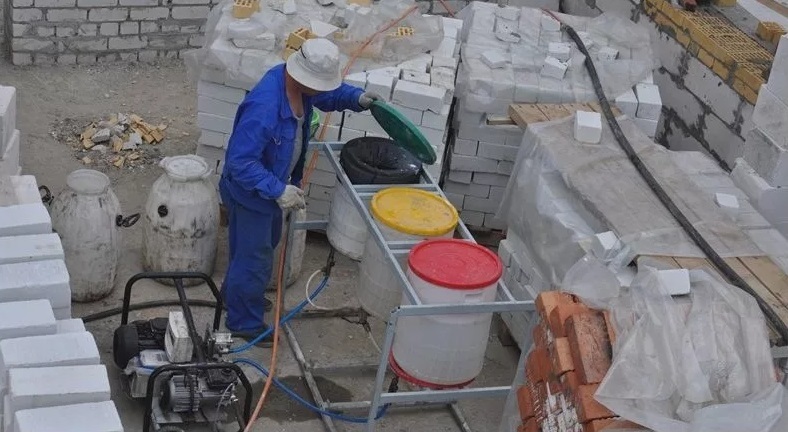
Important! When buying raw materials, pay attention to their smell - a quality product does not have an unpleasant smell.
Other negative properties include:
- Low tensile strength, foam is easy to break after hardening;
- Increased moisture absorption. Sometimes this drawback creates problems, for example, it cannot be used when arranging a screed and when insulating a foundation. You will need to use additional waterproofing;
- The material cannot be manufactured without special equipment;
- Temperature requirements. When pouring foam, the temperature should be above +5 degrees. Without this, high-quality foam cannot be prepared; liquid urea solution sometimes release phenol-formaldehyde. This happens if a low quality resin is purchased.
Important! Outwardly, penoizol is similar to polystyrene, they are often confused when buying. These materials really have a lot in common, the production technology allows you to make foam and foam insulation from the same raw materials. Differences are only in the manufacturing technology.
Several types of material are used for thermal insulation of houses. Their main characteristics are shown in the table.
Common varieties of penoizol | |
Name | Material difference |
Liquid | The most common type. It is used for insulation of any structures and when performing repair work. Fills any gaps and cracks well. It is permissible to prepare the material directly on the construction site. |
Granulated | Produced by grinding polymer raw materials, it is crushed into grains with a section of 10-15 mm. When used economically, granular penoizol in volume is 2 times greater than the volume of material in sheet cutting. Used to fill any voids in flooring and between walls. |
Sheet | Do-it-yourself production of penoizol at home, after which special forms are filled with the solution. After solidification, the material is cut, dried and, if necessary, further processed. Fastened from the outside of the building using dowels. It can be used to fill the voids between the lags. |
Specifications
Penoizol passes water and steam well, so the walls can breathe. The material successfully resists biological degradation. He is not afraid of fungus, microorganisms, he is not even touched by rodents. The material is soft in structure, it adheres tightly to all irregularities, due to which it fills all cracks.
Penoizol was invented recently, for this reason, it is possible to reliably speak about its service life only on the basis of experiments. The manufacturers claim that it is able to withstand approximately 30 years. Another plus is the environmental qualities of the material; during manufacture and operation, it does not emit toxic compounds.
DIY equipment for making penoizol
Nowadays, many devices are being produced for the manufacture of penoizol, among them there is equipment that allows you to make it yourself.
In this case, you can:
- Buy a ready-made unit, which has a gas-liquid installation, the necessary set of taps and a hose for supplying foam. In addition, you will need a compressor and containers for a receiver device with a capacity of 20-300 liters;
- DIY a device that produces penoizol using ready-made drawings.
Used installations for the manufacture of penoizol are not worth buying. The reason is the deterioration of the equipment, which will directly affect the quality of the finished insulation. In addition, the seller does not recognize the condition of the equipment. You can get a lot of problems by purchasing a used rig. Better to buy a new installation right away.
If you decide to use the second option, you will need to find all the components for the production of penoizol:

Equipment is subdivided into construction and workshop equipment. It should be remembered about the important parameters that the installation for penoizol must have:
- Installation of equipment is easy;
- The installation should be easy to use;
- Have the level of performance you need;
- Good mixing of components;
- The ability to change the operating parameters is required;
- It is better to use equipment that is small in size and light;
- High wear resistance is very important.
Important! When choosing a pump, take into account errors in the dosage of components, deviations from the instability of engine speed as a result of load changes and fluctuations.
Having bought a package of documents, the unit can be assembled independently; spare parts are easy to purchase.
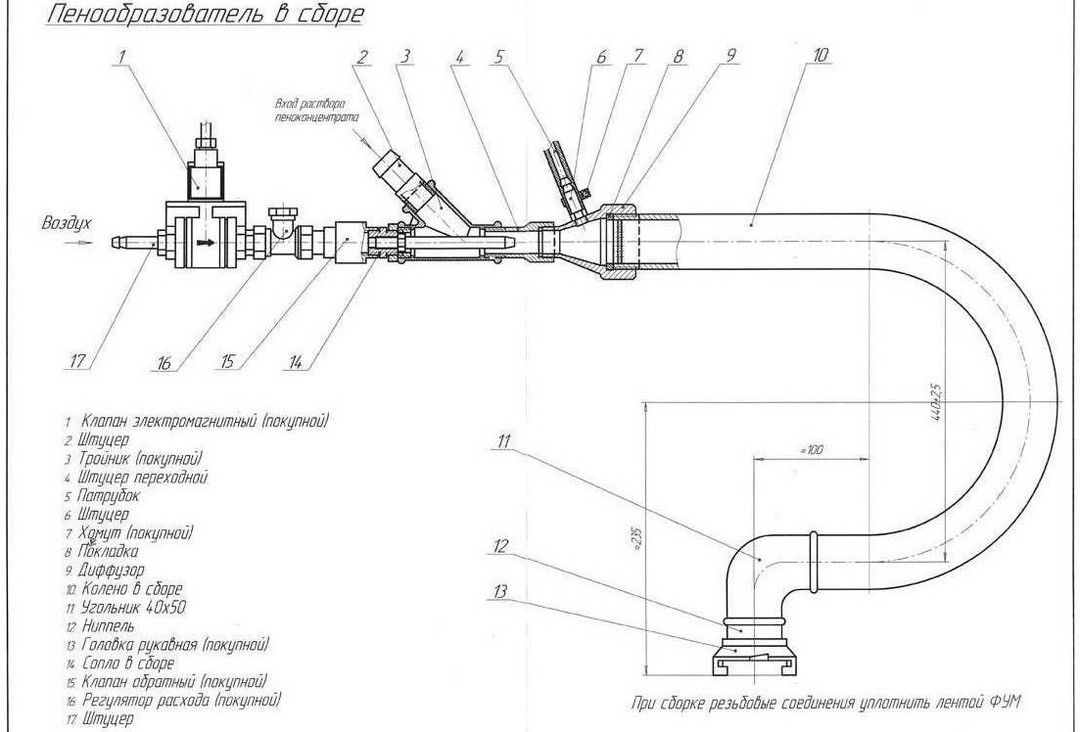
The design, which has the most necessary components, will cost you inexpensively:
- Installation for the formation of bubbles in solution;
- Foam pumping hose;
- Valve;
- Compressor of suitable capacity;
- Materials at hand;
- Barrels with a capacity not exceeding 300 liters.
It is convenient to use vortex or plunger pumps, taking into account the material used in the manufacture of the internal parts. Better if they are plastic, ceramic, stainless steel, or even nickel-plated.
A pump designed for pumping foam to the place of self-insulation is also better to buy a plunger pump. Foam is formed at low pressure in a special generator. In this case, double foaming is more effective, a semi-dry penoizol is obtained at the exit, so it will not simply flow out of the cavity. One pump is installed to supply the resin and the second to pump the foam. along the hose.
The compressor needs sufficient power; when choosing it, the resin consumption is taken into account, which, in order to obtain high-quality material, should not exceed 25 kg.
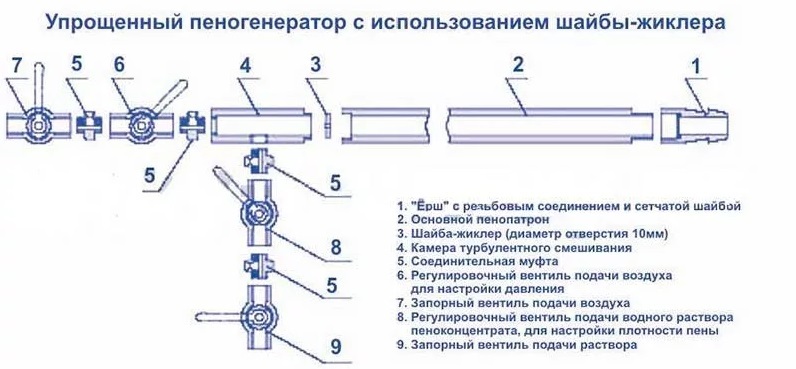
If you need penoizol for your home, then it is convenient to mount the equipment right on the construction site.
First mix a concentrated mixture of a hardener and a foaming agent. For 10 liters of concentrate, 0.25 liters of phosphoric acid and 0.5 liters of a foaming agent are required, everything is diluted in 10 liters with water heated to 60-80 degrees. The solution is well mixed, when there are no clots and lumps in it, then the concentrate is ready, it can be stored in this form for up to 6 months. 1 liter of pre-mixed concentrate is poured into a prepared container of 10 liters of warm water.
Production flow chart and required ingredients
This inexpensive insulation is not difficult to manufacture, since cheap composites are used as raw materials. During production, a semi-liquid foam is made. After it hardens, an elastic material is obtained on which any dents are immediately straightened.
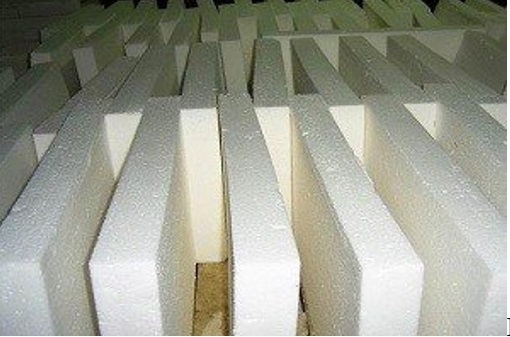
Ingredients for making penoizol are required:
- Urea-formaldehyde resin - the substance from which the foam is made;
- Phosphoric acid - required for foam hardening;
- Foaming agent;
- Water.
The ingredients for the manufacture of penoizol are pumped into the unit by a pump, where they are mixed and foamed with compressed air. After that, the finished product is supplied under pressure to the area that requires protection from the cold.
Freshly made foam resembles white jelly.
The composition hardens after a short time, 10-15 minutes after pumping to the required place from the generator, the foam only slightly grasps, it will reach full strength in 3 days. The solution will fully set after 1-3 days.
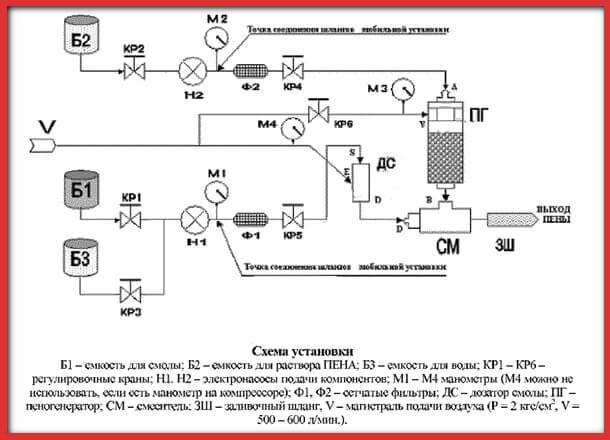
It is necessary to use a compressor of a certain capacity.
If you have high-quality foam with small pores, its contact area will become larger, as a result, the polymerization process will improve. Curing is influenced by the density of the foam. If the density is not enough (the bubbles will be large), then the foam will quickly settle. If this trouble occurs before the main part of the resin has polymerized, then the composition in the mold will simply flow out.
The quality of the foam is affected by the temperature of the water, if it is low, then the material will turn out to be of poor quality. There is a concept - the multiplicity of foam, showing how much product will be obtained from the solution. A high indicator is 60-80, with it you will have 60-80 liters of foam from 1 liter of the prepared solution. You can find out this characteristic if you fill a 200 liter barrel with foam and wait until the bubbles disintegrate. Then the completely settled solution is measured. You can slightly increase foaming by adding more foaming agent to the solution.
Cheaper to order or do it yourself
The production of liquid foam insulation (right at the construction site) allows it to be poured into any voids of the house and for foaming the roof and attic. Or it is produced in solid form, by pouring pre-prepared components after the installation has been foamed into molds. That allows you to lay the finished material in building structures.
The laying speed is several times higher than that of other heaters. It can be used in lightweight designs.