We can no longer imagine life without a knife: they are housewives, hunters, military. Yes, almost everything and everywhere! Find a good knife in the free market is difficult, and models made to order, are very expensive. But it is always possible to do on their own. In this review online magazine HouseChief we'll show you how to make a knife in his home hands, what materials will be required for this, and photos, sketches, videos and step by step instructions greatly facilitate our task.
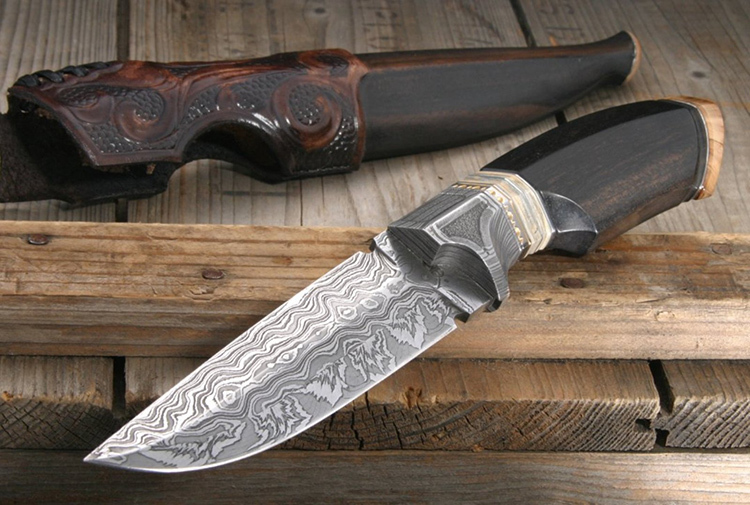
PHOTO: nevseoboi.com.ua
Read article
- 1 A bit of history of the knives
- 2 Constituent elements knife
- 3 Benefits of homemade models
- 4 From what we can opener at home
- 5 Types, features and drawings for knives with their own hands
- 5.1 Knives for hunting
- 5.2 Kitchen knives
- 5.3 Knives for tourism and survival
- 5.4 fighting knives
- 6 Stages of manufacture of the knife with his hands
- 6.1 Sketches and Drawings
- 6.2 Selection of a steel billet knife
- 6.3 How do knives
- 6.3.1 How to make blade
- 6.3.2 How to make a pen knife
- 7 How to make a knife out of a tree
- 8 How to make a sheath for a knife with his hands
A bit of history of the knives
The first knives scrapers can be considered, from the bones of animals and stones, made by primitive people. These guns were good for those times, but their production was spent a lot of effort. In addition, they were either fragile or fast tupilis. Once a person has mastered metalworking primitive knives and weapons began to create in bronze and copper. With the development of technology to replace these metals came iron and steel. This allowed to make blades more durable and long-lasting. Also, a variety of designs and form of knives, daggers, swords and other thrusting and cutting tool.
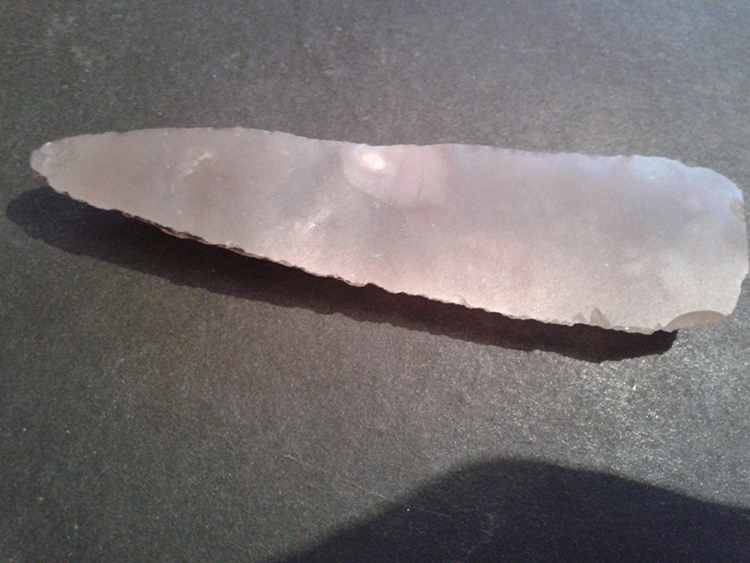
PHOTO: pics.meshok.net
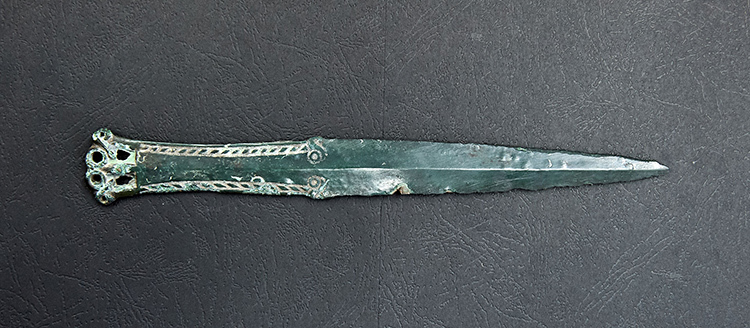
PHOTO: newslab.ru
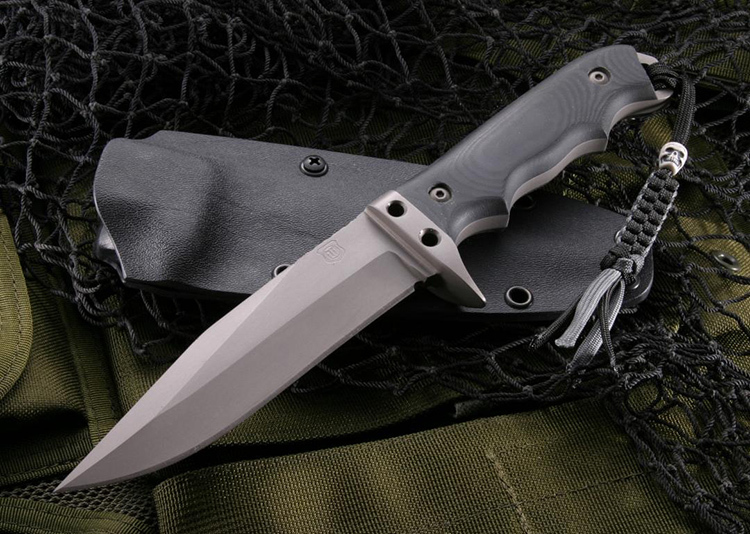
PHOTO: popgun.ru
Constituent elements knife
Knives can have very different purpose, shape and design, but all of their common elements are combined. The most important of them - the blade shank or handle. In turn, the blade is divided into: The tip or nose, butt, cutting edge or blade, the heel. The shank consists of tops, limiter and facing.
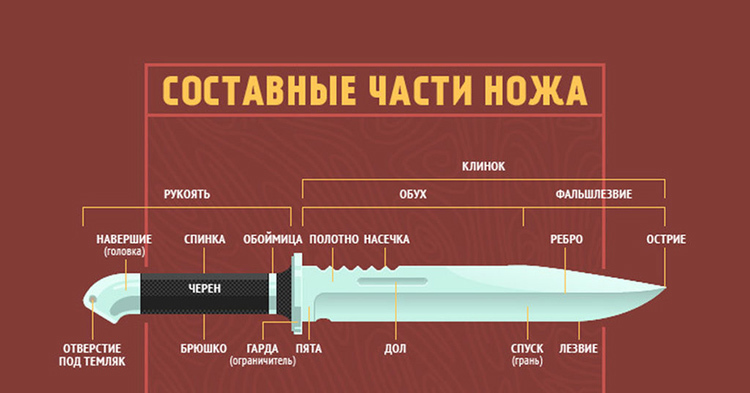
PHOTO: ikarp.ru
Benefits of homemade models
The modern market is swamped with a large assortment of the most diverse knives, but they do not always meet the requirements of the consumer. In addition, often the products of most manufacturers do not is of good quality material and workmanship. You can order the required quality and the blade shape by a specialist, but this product will cost quite expensive. But if you are not passionate collector of knives, and you are only interested in the practical side of the issue, it is possible to make a knife with his hands.
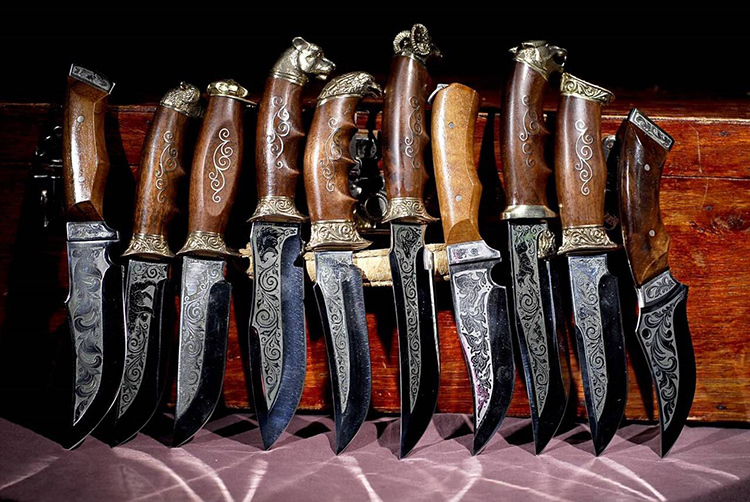
PHOTO: tver-ohota.ru
Hand made home-made knives have several advantages:
- Blade type corresponds to the needs of the owner;
- combine all the necessary properties and characteristics;
- independent choice of an appropriate grade of steel;
- hardening and metal release for improving the strength characteristics;
- Manufacturing under the anatomical features of the holder;
- the selection of blade design and the handle in accordance with their own ideas about the aesthetics of a knife;
- possible to prevent the defects present in shirpotrebovsky models.
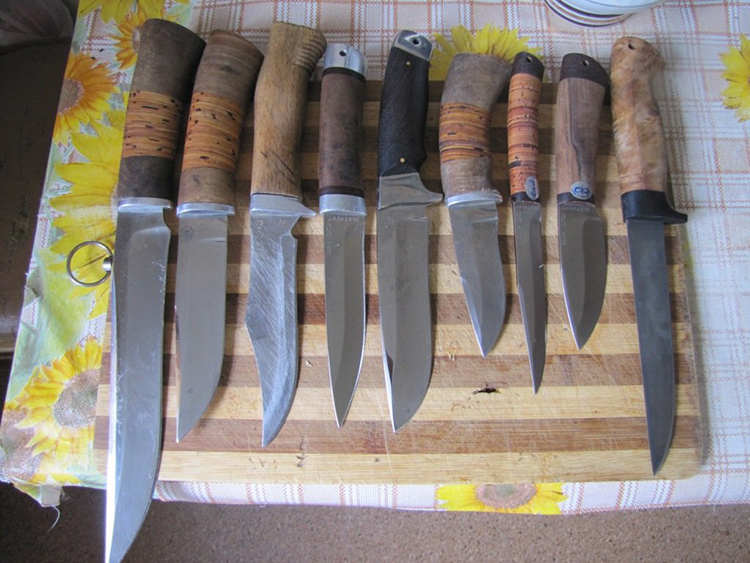
PHOTO: avatars.mds.yandex.net
From what we can opener at home
Purpose and knife design largely determines the material for its production. The best were considered blades made of damask and Damascus steel, but it can not make even a seasoned master blacksmiths. You can purchase a strip of high-quality metal, but its price can be quite high.
In order to make a knife with his hands in the home, often using old files, depreciation spring steel strips or pieces of circular saws. It is the most affordable option, because the only machining required for the manufacture of the blade. You can also make a knife out of wood, plastic or plexiglass, but talk about it below.
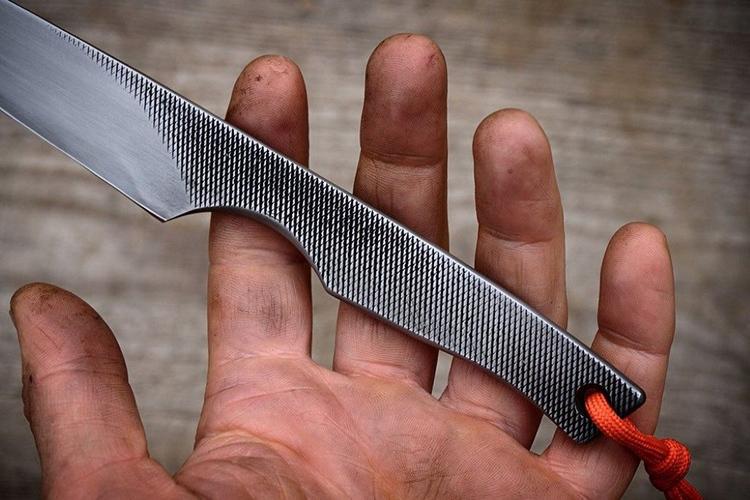
PHOTO: i.pinimg.com
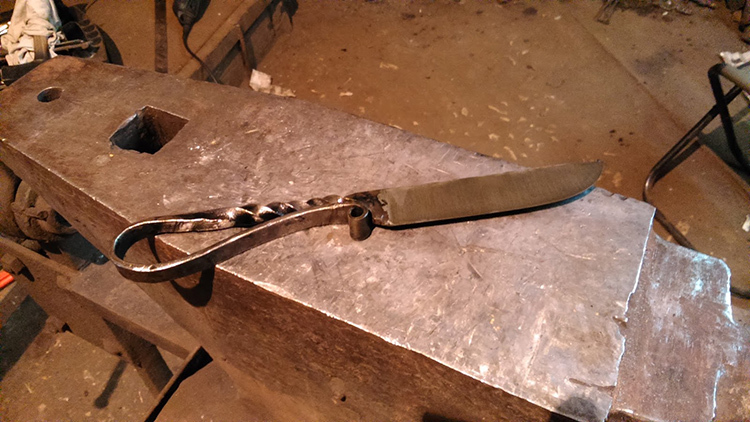
PHOTO: 3.bp.blogspot.com
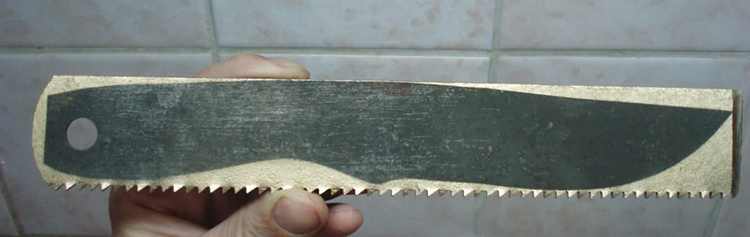
PHOTO: pohod-lifehack.ru
Types, features and drawings for knives with their own hands
There are many types of knives, with different applications. From the scope of application of the blade depends on its design, the shape, the material for manufacturing, strength properties, and more. Consider the main types and designs of knives for self-manufacturing, depending on their destination.
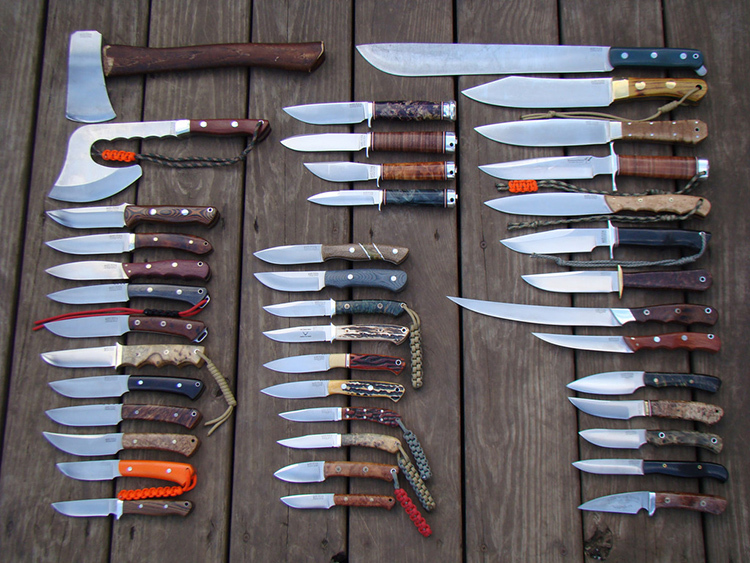
PHOTO: popgun.ru
Knives for hunting
This is probably the most ancient and popular form of knives. Hunting knives were used to fight with a wild animal, and cutting production. They always have high demands:
- easy handling;
- It must be high-quality steel, wear-resistant and long time to keep sharpening. Best, though expensive option - Damascus steel or damask;
- the handle is made only of solid wood;
- no need for a large garde, interfering butchering;
- Optimal parameters: length and width of the blade - 100-140 × 30 mm butt - 3.4 mm and the hardness of steel is not less than 58 HRC.
All of these characteristics must be considered, making hunting knife with his hands. Blades for hunting are often proud owner. They are decorated with thematic scenes, patterns, and the handle is made from bones of wild animals. Some hunters gather a collection of knives.
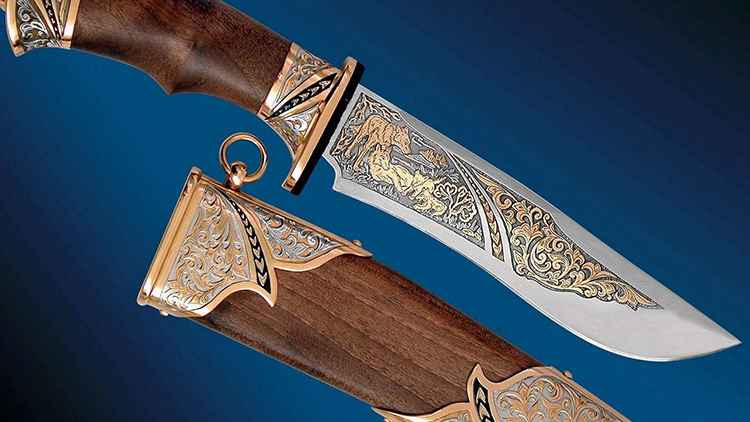
PHOTO: rusknife.com
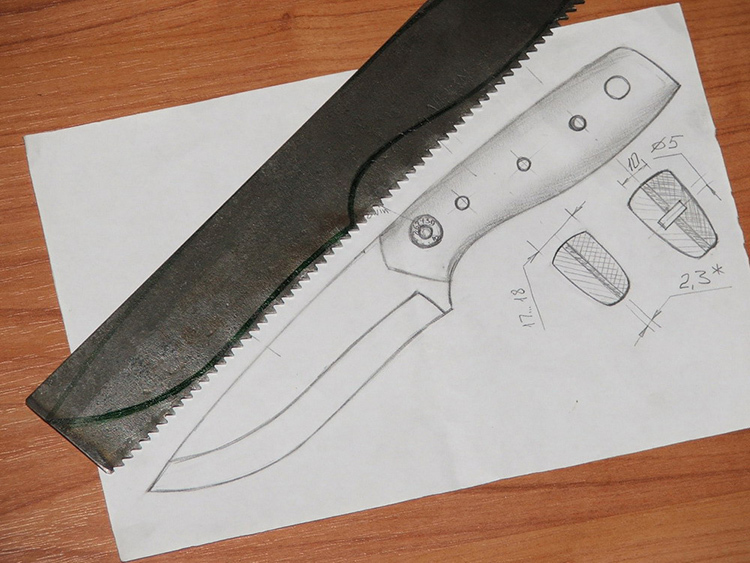
PHOTO: popgun.ru
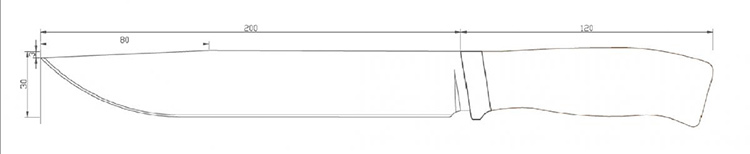
PHOTO: rusknife.com
Watch a video on how to make a hunting knife with his hands at home.
Kitchen knives
Knife - a compulsory subject for any kitchen. They are housewives and chefs renowned restaurants. To perform daily tasks quite 3 knives, but there are a set of more than 10 items, each designed for a specific work: cutting vegetables, meat, bread, etc.
For the manufacture of kitchen originally used metal blades, which are subject to certain requirements. It should be firm, not oxidized and is suitable for home sharpening. Contemporary blades are now manufactured and ceramics. These models are characterized by high hardness, long retain the factory grinding, but they are quite fragile and can break if dropped on a ceramic tile or cement surfaces. Facing handle household kitchen knives are mainly made of plastic, but also applies a solid hardwood.
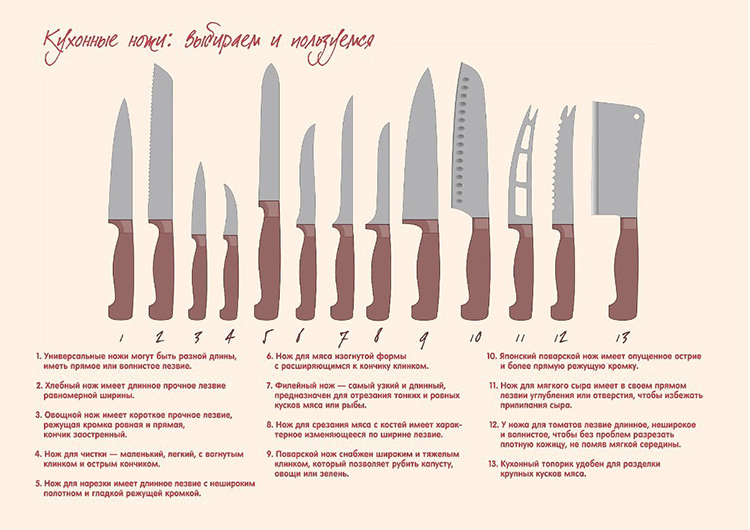
PHOTO: aggweb.ru
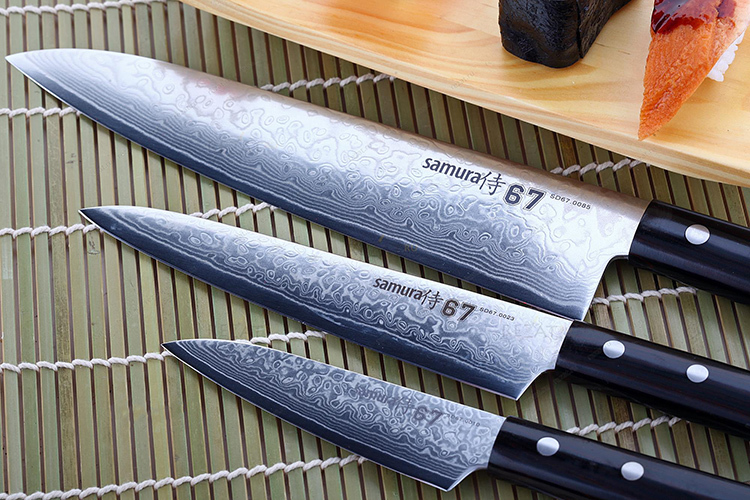
PHOTO: img.best-kitchen.ru
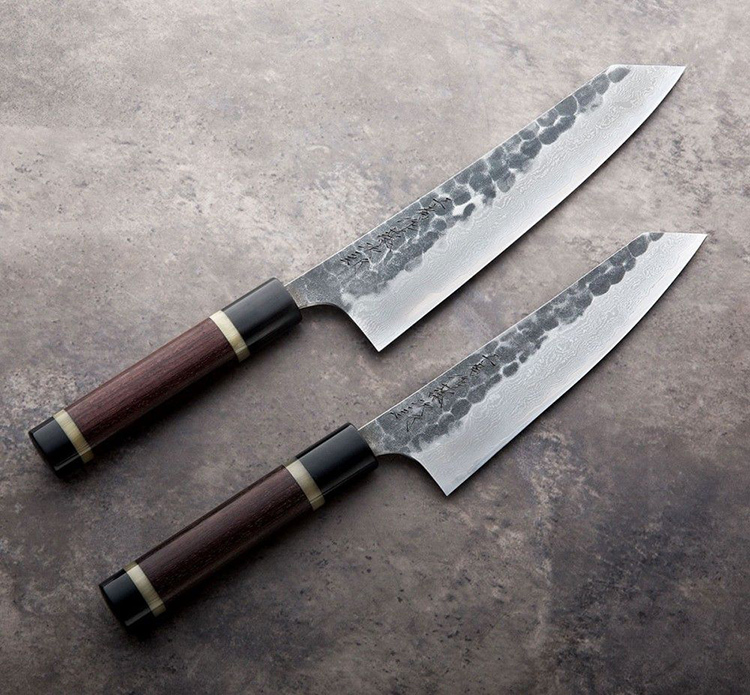
PHOTO: i.pinimg.com
Knives for tourism and survival
Backpacking or fishing can not do without a good knife. Going to the nature, often have to deal with various problems, which will help to solve a quality, properly sized blade. Good tourist knife - is:
- possibility easily to cut threads of different thicknesses, cut slings and ropes;
- necessarily a fixed blade;
- wide thick blade and handle;
- the blade must be made of a soft stainless steel for easy grinding in field conditions;
- handle made of plastic, rubber and ribbed to prevent slipping.
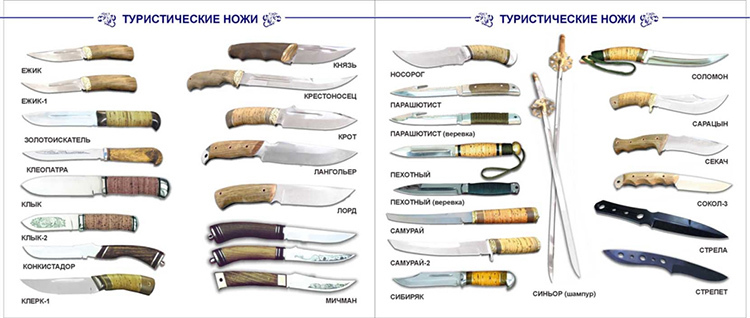
PHOTO: rusknife.com
survival knives are derived from travel models. They additionally completed with special devices (Multitools), which should help a person in extreme conditions. However, often due to the pursuit of maximum quality of the product suffers versatility.
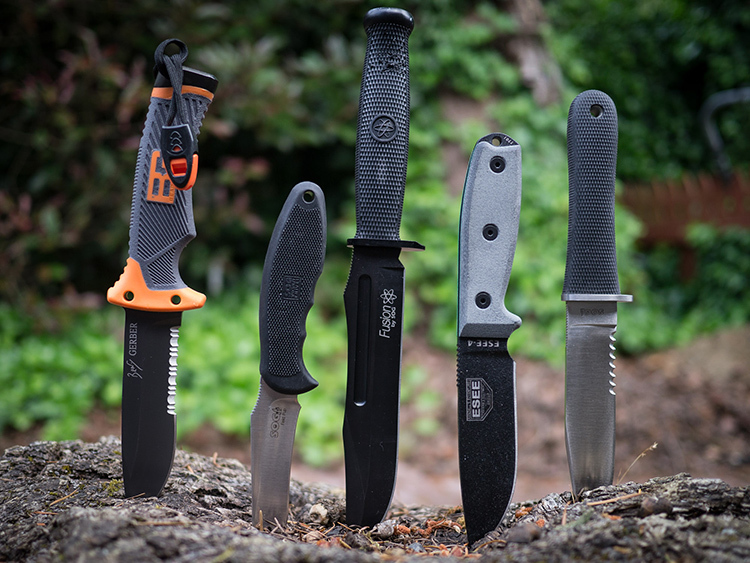
PHOTO: outlivetheoutbreak.com
fighting knives
Combat is considered a knife designed to engage the enemy in close combat, was in service in the armies of different countries. In addition to performing basic tasks, such blades may be used to entrenchment, barbed wire cutting, cutting branches, etc. The distinctive features of the knives used by the military, are:
- or bilateral sharpening queen;
- oval cross-section the handle;
- the length of the whole product is 220-320 mm;
- spearhead in line with the butt of the handle and the blade;
- reinforced guard;
- extracting easy one-handed;
- anti-reflective coating.
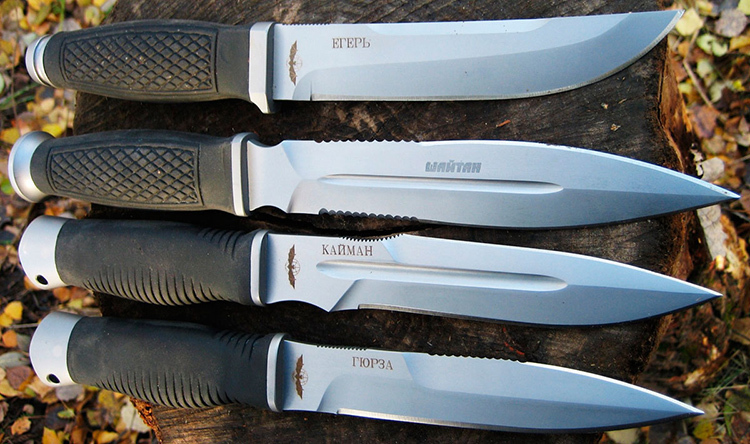
PHOTO: unpictures.ru
Stages of manufacture of the knife with his hands
Done by hand knife is not a problem. You do not even need a lot of tools. To create a simple blade will need a strip of steel hacksaw and file. But more about that later, but for now we will consider the steps of manufacturing the blade with your hands, drawings and materials.
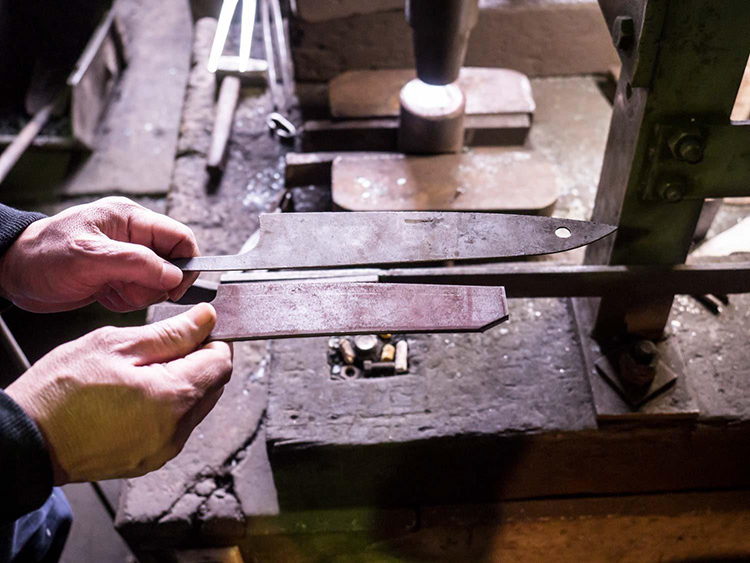
PHOTO: cdn3.hype.ru
Sketches and Drawings
Deciding to make a practical and beautiful knife with your hands, you must first decide on its purpose: tourism, hunting or for the cuisine. It largely determines the choice of the shape of the blade, its design and material. Next is a sketch of the knife, as you imagine it represent. Based on it created a drawing with dimensions. If you have no artistic talent or knowledge in the arms business, and make the blade really want, you can use ready-made ideas from the Internet. The photo presented drawings and shapes of knives.
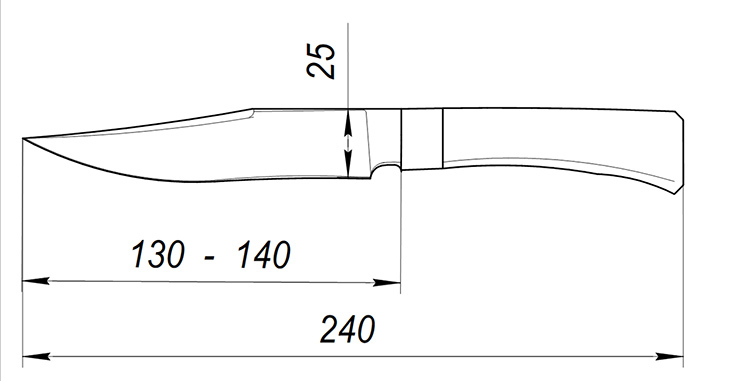
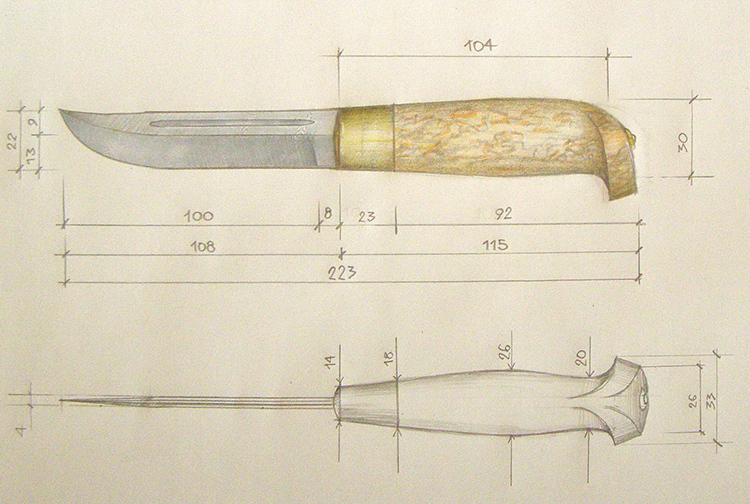
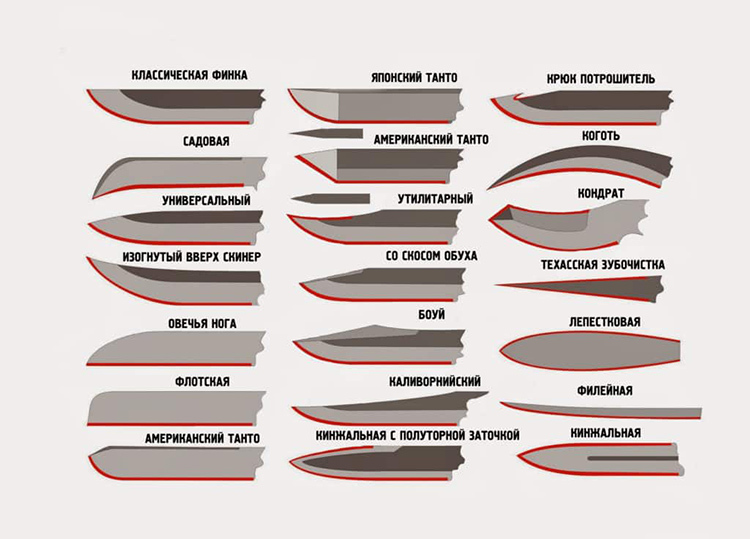
Selection of a steel billet knife
Decide on the type of knife, make a sketch and drawing, you can proceed to the selection of the workpiece. different grades of steel are used for the manufacture of the blades. The choice depends on the purpose of the knife:
- 95X18. The most popular and common type of steel for the manufacture of the blades. Its advantage lies in the high strength and corrosion resistance even at a high rate of hardness 64 HRC. After heat treatment the preform to a value of 62 HRC, the cutting edge of the blade is almost completely protected from chipping due to collisions with the solid surface.
- 50H14MF. Another popular type of steel used for the production of blades. This is one of the best materials of construction for the medical scalpels. Mark provides hardness to 58 HRC, and long-term preservation of sharpening.
- H12MF. This steel grade has good toughness and after appropriate heat treatment acquires hardness to 62 HRC. Blade sharpening blade keeps well, it is not fragile, but it is subject to corrosion. Knives of this alloy needs special care.
- CVH. Steel grade relating to the tool and having a good hardness with excellent toughness, which allows the blade does not break when a serious blow.
- 50HGA. Spring steel, which is an excellent material for knives, used in extreme conditions and at high loads. The disadvantage is the susceptibility to corrosion.
- 40X13. Also refer to the spring steel, but unlike the previous mark, impervious to corrosion. Often used to make knives, but quickly blunts the cutting edge.
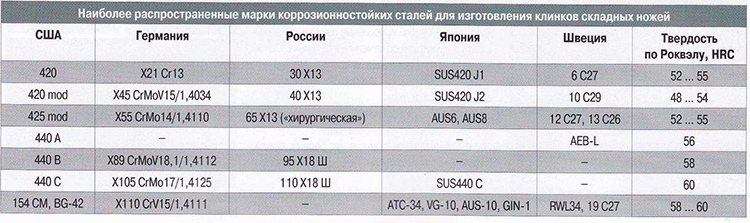
PHOTO: i0.wp.com
Watch a video on the topic of choice for steel knife:
How do knives
After the selected type of blade is made a sketch drawing and acquired the desired grade steel, can proceed to the manufacture of the blade. According to the outline of the pattern to be produced from cardboard or plywood. The latter option is good if you intend to do more than one knife. Now, when everything is ready, you can start making blade.
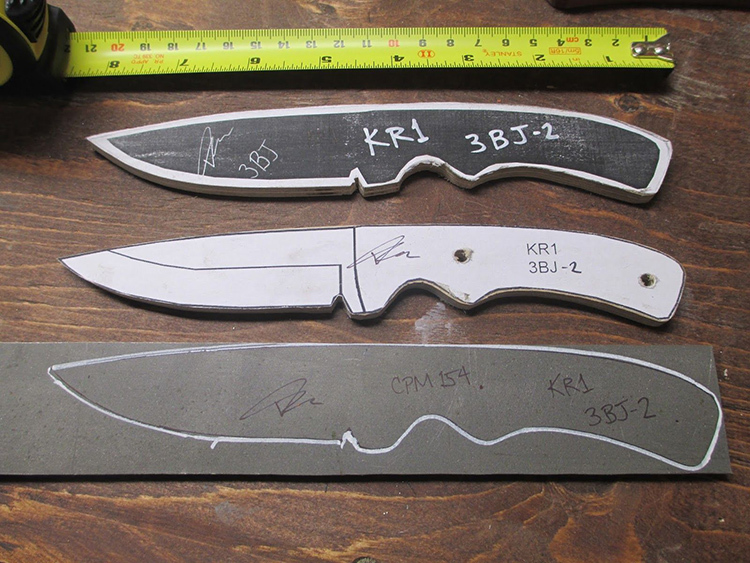
PHOTO: i.pinimg.com
How to make blade
knife blade made in two steps: mechanical and heat treatment. In some cases, metal heat treatment is impossible, and it worsens the qualitative characteristics of the product. To get started on the workpiece is necessary to impose a template and cut around the contour of the future knife. In industrial scale the blades are cut by laser, gas cutting or milling machine. At home, the knife can be cut along the contour with the help of hacksaws for metal or "Bulgarian" with a cutting disc. To the desired size blade is brought to emery machine. On it also induced blade border, and performed initial rough grinding.

PHOTO: i.ytimg.com
Once formed into the desired preform shape, it is advisable to carry out quenching and metal accommodation in accordance with the technology indicated in the references for metalworking. If you can not control the temperature regime with the help of special equipment, you can navigate by incandescence, but in this case will require assistance of an experienced specialist. Rigorously conducted hardening and tempering the metal will significantly improve the strength characteristics of the knife.
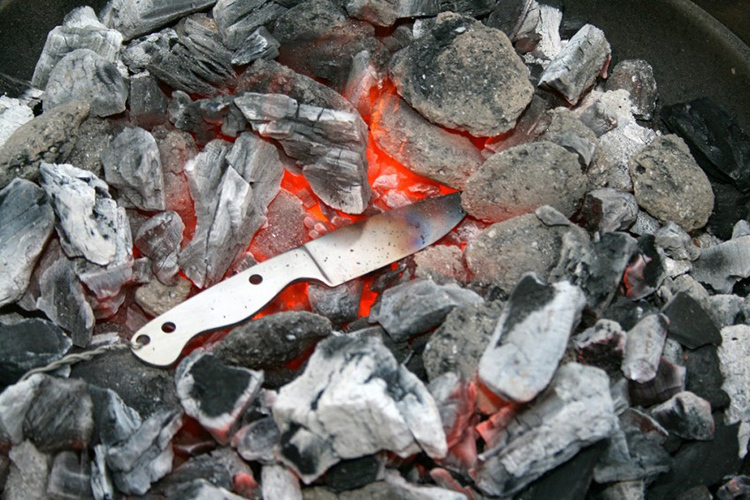
PHOTO: tytmaster.ru
How to make a pen knife
Once the blade is ready, the question arises: what and how to stick to the knife. The handle may be a bill or the push-manufactured from plastic or solid wood. The simplest handle - tail coiled strip of strong thick skin. Waybill handle is made of two plates of plastic or wood, which are attached to the shank by means of rivets inserted into pre-drilled holes. After fixation, lining, on sandpaper or abrasive paper of various grit handle is brought to the desired shape and smoothness.
The video shows how to do push-handle knife:
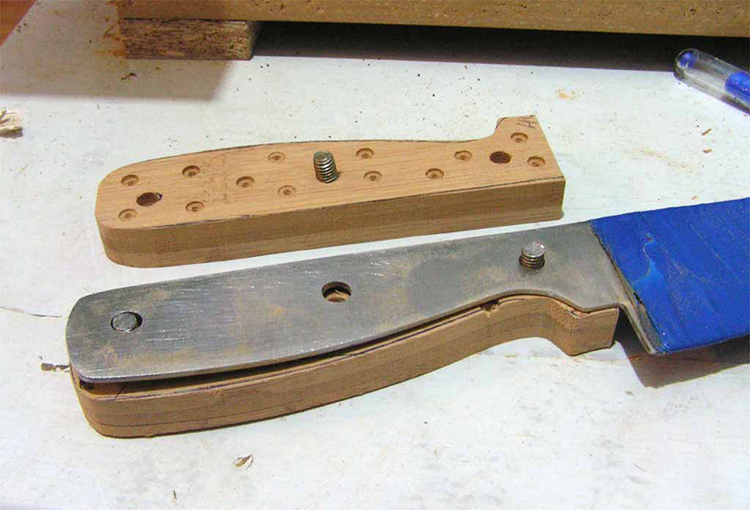
PHOTO: popgun.ru
Watch the video, how to make a knife with his hands in the home:
How to make a knife out of a tree
We have seen how the blades are made of steel, and now know how to make a wooden knife. As is the case with a steel knife, you need to prepare a template, pick up a piece of solid wood boards and tools. It needs a jigsaw or hacksaw on wood sander or a set of sandpaper with different grits.
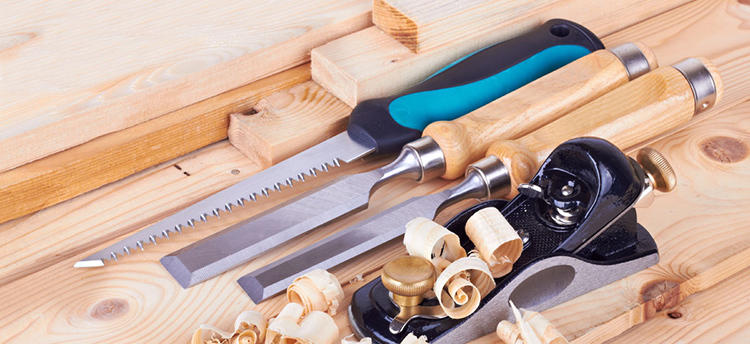
PHOTO: eastwoodscarpentry.co.uk
Picture | Process description |
![]() | To begin, take a piece of board of firm and solid wood. By hand or draw a pattern outline the future of the knife |
![]() | The machine, cut with a hacksaw or jigsaw blade blank |
![]() | At the narrow part also direct the profile contour. Remove all unnecessary |
![]() | I should get here this blade. But he was still, so to speak, a "raw" |
![]() | Grind using the disc grinder with a special |
![]() | Round off the edge of the handle, you can use the hand router |
![]() | Sharpen the blade on a belt sander. This work is to be performed very carefully, since the hard-pressed or wrong movement of the workpiece easily spoil. Then you have to start all over again |
![]() | Again grind |
![]() | Knife cover molten metal and allowed to dry for at least for 12 hours. Who wants, can skip this step |
![]() | After drying the liquid metal back grind the workpiece |
![]() | After polishing take mineral oil |
![]() | Swab well impregnate knife mineral oil |
![]() | It should look like the picture |
![]() | And, of course, test opener |
This wooden knife, of course, no substitute for a full-fledged kitchen metal model, but to cut vegetables, fruit, cake, cheese or oil can easily.
How to make a sheath for a knife with his hands
Sheath - a mandatory attribute of any blade, except household kitchen knife. They protect it from moisture, dirt, breaks, bluntness, protecting the wearer from accidental injury. Sheath may be made of plastic, leather or wood, and can be combined models. Most blades are sold with a protective case, but for homemade blades will have to create their own sheath.
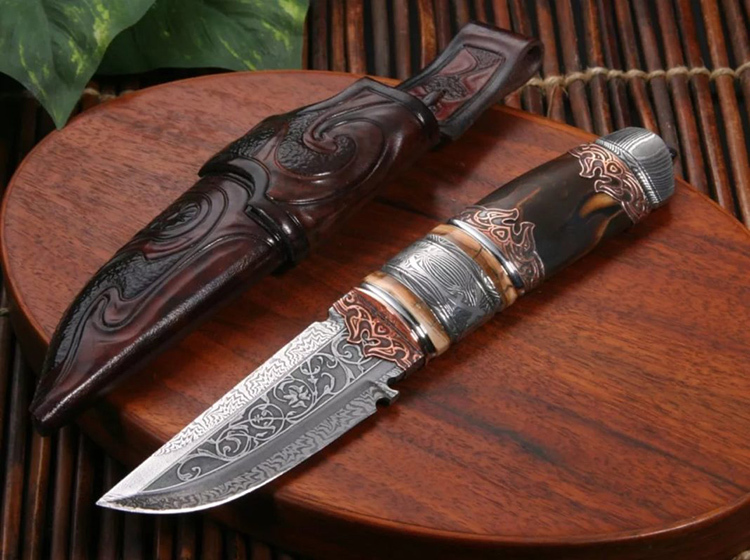
PHOTO: travelnews24.ru
The video shows a gradual process of manufacturing leather sheath with a liner made of larch. Watch this video, you will understand that this is no big deal: just have to diligence, care and patience.